Metal laser cutting technology is one of the most widely used techniques in modern metal cutting, capable of cutting materials such as steel, aluminum, stainless steel, and other metals. Additionally, laser cutting is often used for metal sheet cutting, allowing for various shapes to be cut with high precision and fast speed. Laser cutting technology is also very suitable for customized cutting needs.
In laser cutting technology, cutting precision and cutting speed are among the most critical factors. Cutting precision refers to the smallest cutting dimension that can be achieved during the cutting process, which typically reaches a very high level of accuracy, meeting the needs for high-demand cutting applications. Cutting speed refers to the thickness of the metal material that can be cut within a certain time frame, and laser cutting speed is usually faster than traditional cutting methods.
In summary, laser cutting technology is an indispensable technique in modern metal cutting, especially in the cutting of steel, aluminum, stainless steel, and metal sheets. When performing laser cutting, cutting precision and cutting speed are two of the most important factors, and adjustments can be made based on the specific needs.
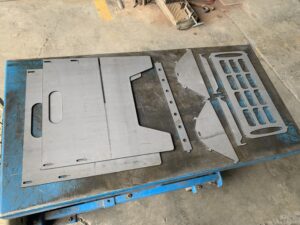
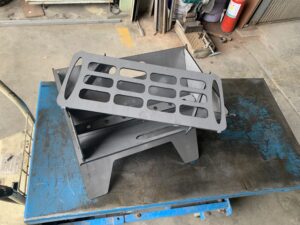
The 7 types of steel cutting are the most common applications in laser cutting outsourcing technology:
- Carbon Steel
Modern laser cutting systems can cut carbon steel plates with a maximum thickness of up to 20mm. By using the oxidation-melting cutting mechanism, the cut gap can be controlled to a satisfactory width, and for thin plates, the gap can be narrowed to about 0.1mm. - Stainless Steel
Laser cutting is an effective processing tool for industries that use stainless steel thin plates as the main components. With strict control over heat input during the laser cutting process, the thermal impact zone at the cutting edge can be minimized, effectively preserving the material’s good corrosion resistance. - Alloy Steel
Most alloy structural steels and alloy tool steels can achieve good edge quality with laser cutting. Even for some high-strength materials, if the process parameters are well controlled, straight, slag-free cuts can be obtained. However, for tungsten-containing high-speed tool steels and hot mold steels, laser cutting may lead to melting and slag attachment. - Aluminum and Alloys
Aluminum cutting belongs to the melting cutting mechanism, where the auxiliary gas is mainly used to blow away the molten products from the cutting area, typically resulting in a better surface quality. For some aluminum alloys, special care must be taken to prevent the formation of intergranular micro-cracks in the cut surface. - Copper and Alloys
Pure copper (red copper) has a very high reflectivity and cannot be cut using a CO2 laser beam. Brass (copper alloys) can be cut using higher laser power with auxiliary gases such as air or oxygen, allowing for cutting of thinner sheets. - Titanium and Alloys
Pure titanium couples well with the focused laser beam to convert thermal energy. When oxygen is used as an auxiliary gas, the chemical reaction is vigorous, leading to faster cutting speeds, but it may create an oxide layer at the cutting edge and cause overheating if not properly controlled. For stability, air is often preferred as the auxiliary gas to ensure cutting quality. Laser cutting of titanium alloys, commonly used in the aerospace industry, generally results in good quality, although slight slag may form at the cut bottom, which is easy to remove. - Nickel Alloys
Nickel-based alloys, also known as superalloys, are available in many types. Most of these can be processed using the oxidation-melting cutting method.
Checking Surface Quality and Positioning Dimensions
For industrial aluminum profile cutting, besides determining the length and verifying dimensions, careful inspection of surface quality and positioning dimensions is essential. Defective or substandard aluminum profiles should be marked and the defects should be cut out before the main cutting to ensure the smoothness and quality of the surface after cutting. Furthermore, to avoid secondary processing and improve production efficiency, professional aluminum profile cutting machines should be selected to ensure accuracy and stability during the cutting process. Only by emphasizing surface quality and positioning dimension checks can high-quality industrial aluminum profiles be produced.
Attention to the Operating Condition of the Aluminum Profile Cutting Machine
When cutting aluminum profiles, the operation status of the cutting machine and the quality of the saw blade should be closely monitored. For the machine’s operating condition, check if the motor is overheating, if there are unusual noises or odors, if the downward pressure indicator is normal, and if the lubrication system is properly installed. These factors directly affect the cutting quality and accuracy of the aluminum profiles. Therefore, maintenance personnel should conduct regular inspections to ensure the machine operates well. Additionally, attention should be given to the selection of saw blade quality, especially when cutting thin-walled aluminum pipes, where blades with more teeth and minimal material deformation are preferred. Addressing these issues ensures the cutting quality and accuracy of aluminum profiles.
Precision Issues: Length, Angle, Drilling, and Tapping
In the processing of aluminum profiles, precision is extremely important. Length, angle, drilling, and tapping are common areas of concern. Length cutting typically involves cutting 6-meter-long aluminum profiles to the required length. Angle cutting occurs on conveyor line equipment and door frame structures, where strict control over angles is necessary. Drilling and tapping are standard steps in aluminum profile processing and are crucial to ensuring product quality. For process precision, the smaller the error, the better. Solving these precision issues not only improves the efficiency of the production process but also ensures the stability and consistency of the final product’s performance. By addressing these issues, the quality of aluminum profile processing can be significantly improved.

Advantages of Industrial Aluminum Profiles in Production and Use
The production and use of industrial aluminum profiles offer numerous advantages, particularly in meeting industrial needs. These profiles are designed with high material quality, strength, and tolerance requirements, which makes their production more challenging and technically demanding. The key advantages of industrial aluminum profiles lie in their broad range of applications. They are widely used in areas such as automation machinery, equipment housings, conveyors, lifts, assembly lines, and the medical industry.
Moreover, the high strength, low density, and corrosion-resistant properties of aluminum make it an ideal material choice for these applications. Therefore, when selecting aluminum profiles, it is essential to consider both the production quality and the background of the manufacturer to ensure the material’s durability and reliability.
In practical use, it is also important to maintain and clean aluminum shavings to ensure the proper functioning of the equipment. In conclusion, industrial aluminum profiles offer substantial advantages in various applications, especially due to their excellent performance in terms of high strength, low density, and corrosion resistance.