目錄大綱
- 1 Common Steel Cutting Methods: Flame Cutting, Plasma Cutting, Laser Cutting, and Water Cutting
- 2 Flame Cutting
- 3 Plasma Cutting
- 4 Water Cutting
- 5 Mechanical Cutting
- 6 Laser Cutting
- 7 Why Laser Cutting is the Preferred Method for Steel Cutting
- 8 Fast and Efficient
- 9 High Precision and High Quality
- 10 Can Cut Various Materials
- 11 Understanding the Steel Laser Cutting Process
- 12 Leveraging the Advantages of Steel Laser Cutting Manufacturers
- 13 Using Steel Laser Cutting for Different Types of Steel
- 14 Aluminum Laser Cutting
- 15 Stainless Steel Laser Cutting
- 16 Copper Laser Cutting
- 17 Brass Laser Cutting
- 18 Factors Affecting Steel Cutting Speed
- 19 Advantages and Disadvantages of Different Metal Laser Cutting Methods
- 20 Cutting Quality Requirements
- 21 Choosing the Right Steel Cutting Service Provider
- 22 The Future of Steel Cutting: Why Laser Cutting is the First Choice
- 23 Higher Efficiency and Quality
- 24 Higher Flexibility and Adaptability
- 25 Higher Environmental Friendliness and Safety
- 26 Conclusion
am a manufacturing worker with ten years of experience. Throughout my career, I have used many different methods for cutting steel. Each method has its pros and cons, but ultimately, I found that laser cutting is the best choice. In this article, I will share knowledge and experiences about steel cutting and why laser cutting is the best option.
The Importance of Choosing the Right Steel Cutting Method
In the manufacturing industry, steel cutting is a very common task. Different types of steel require different cutting methods, and choosing the right cutting method ensures the quality and efficiency of the product. A wrong choice could result in inaccurate part dimensions, rough cutting edges, and even potential damage to the steel. Therefore, choosing the correct steel cutting method is crucial.
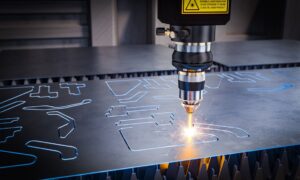
Common Steel Cutting Methods: Flame Cutting, Plasma Cutting, Laser Cutting, and Water Cutting
There are many methods for steel cutting, such as flame cutting, plasma cutting, water cutting, mechanical cutting, and laser cutting. Each method has its advantages and disadvantages. Below are some common steel cutting methods and their pros and cons:
Flame Cutting
Flame cutting is a common method for cutting steel. Its advantages include low cost and suitability for thicker steel plates and large parts. The disadvantages are slower cutting speed, lower precision, and the generation of heat-affected zones, which can cause deformation.
Plasma Cutting
Plasma cutting is a high-speed, high-precision cutting method. Its advantages are fast cutting speed, high precision, and no heat-affected zones. The disadvantage is that it is more expensive and is only suitable for thinner steel plates and small parts.
Water Cutting
Water cutting is a method that uses high-pressure water jets to cut steel. Its advantages include no heat-affected zones and the ability to cut many different materials. The disadvantages are slower cutting speed and lower precision.
Mechanical Cutting
Mechanical cutting is a traditional method for cutting steel. Its advantages are low cost and suitability for many different materials. The disadvantages are slower cutting speed, lower precision, and susceptibility to deformation.
Laser Cutting
Laser cutting is a high-speed, high-precision cutting method. Its advantages are fast cutting speed, high precision, and no heat-affected zones. The disadvantage is its higher cost and its suitability only for thinner steel plates and small parts.
Why Laser Cutting is the Preferred Method for Steel Cutting
Although there are many different methods for steel cutting, laser cutting is the best choice for several reasons:
Fast and Efficient
Laser cutting is a high-speed, efficient cutting method. It can quickly cut parts with high precision and smooth surfaces, significantly reducing production cycles.
High Precision and High Quality
Laser cutting can cut without generating heat-affected zones, ensuring the accuracy and quality of the parts. It also allows for intricate details to be cut, making it suitable for high-precision parts.
Can Cut Various Materials
Laser cutting can cut almost all materials, including steel, aluminum, stainless steel, copper, brass, and more. This makes it a very flexible cutting method.
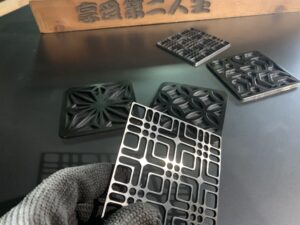
Environmental and Safety Considerations
Laser cutting is an environmentally friendly and safe cutting method. It does not produce waste gas, wastewater, or waste residue, and it does not generate noise or radiation. This makes it a very popular cutting method.
Understanding the Steel Laser Cutting Process
The process of laser cutting is very straightforward. After setting the cutting parameters on the laser cutting machine, the laser beam cuts according to the design pattern. During the cutting process, the laser beam heats the steel to its melting point and uses a gas flow to blow away the molten material, thereby forming the desired shape.
Leveraging the Advantages of Steel Laser Cutting Manufacturers
If you need steel cutting, I recommend choosing a professional laser cutting manufacturer. These manufacturers have advanced laser cutting equipment and experienced technicians who can ensure the quality of your parts and delivery times.
Moreover, laser cutting manufacturers also offer other services such as design, processing, and assembly, providing you with comprehensive manufacturing solutions.
Using Steel Laser Cutting for Different Types of Steel
Steel laser cutting can be used for cutting many different types of steel, including aluminum, stainless steel, copper, brass, etc. Here are some common types of steel laser cutting:
Aluminum Laser Cutting
Aluminum laser cutting is a very common cutting method. It can cut precise and smooth aluminum plates and profiles, suitable for various applications.
Stainless Steel Laser Cutting
Stainless steel laser cutting is a high-precision, high-quality cutting method. It can cut precise and smooth stainless steel plates and profiles, suitable for high-precision parts.
Copper Laser Cutting
Copper laser cutting is a very versatile cutting method. It can cut copper plates and profiles, suitable for various applications.
Brass Laser Cutting
Brass laser cutting is an efficient and high-quality cutting method. It can cut precise and smooth brass plates and profiles, suitable for various applications.
Factors Affecting Steel Cutting Speed
The speed of steel cutting depends on many factors, such as material thickness, cutting quality requirements, machine model, and cutting parameters. Below are some common factors that affect steel cutting speed: Material thickness is an important factor affecting steel cutting speed. Generally, the thicker the material, the slower the cutting speed.
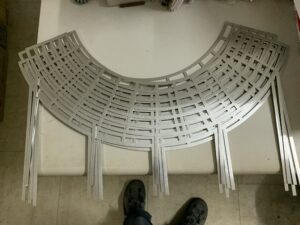
Advantages and Disadvantages of Different Metal Laser Cutting Methods
Cutting Method | Advantages | Disadvantages |
---|---|---|
Steel Plate Laser Cutting | High cutting precision, fast cutting speed, less deformation | Limited cutting thickness, high equipment cost |
Steel Material Cutting Processing | Can be used for cutting various shapes of steel | Generates a lot of chips and dust |
Aluminum Laser Cutting | Fast cutting speed, high cutting quality | Can damage equipment, limited cutting thickness |
Stainless Steel Laser Cutting | High cutting quality, smooth cuts, no burrs | Limited cutting thickness, high equipment cost |
Steel Laser Cutting | High precision, fast speed, can cut complex shapes | High equipment cost, limited material thickness |
Steel Cutting | Suitable for various steel thicknesses | Cutting precision is lower than laser cutting, generates a lot of chips and dust |
Note: These advantages and disadvantages are general for each cutting method. The specific situation should consider the actual application needs and equipment technology level.
Cutting Quality Requirements
Cutting quality requirements are also a factor that affects steel cutting speed. If high cutting quality is required, the cutting speed will decrease accordingly. The cutting machine model and parameters also affect the steel cutting speed. Different models of cutting machines have different cutting capabilities, and different cutting parameters can influence cutting speed.
Choosing the Right Steel Cutting Service Provider
If you need steel cutting, I recommend choosing a professional steel cutting service provider. These providers have advanced equipment and experienced technicians to ensure your parts’ quality and delivery time. Additionally, they also offer other services such as design, processing, and assembly, providing a comprehensive manufacturing solution.
The Future of Steel Cutting: Why Laser Cutting is the First Choice
With the continuous development of manufacturing technologies, steel cutting technologies are also improving. While there are many different steel cutting methods available, laser cutting is the trend of the future. Here are a few reasons why:
Higher Efficiency and Quality
As laser cutting technology continues to improve, it will become faster and more efficient. Additionally, with the continuous development of materials science, laser cutting will be able to cut more materials, improving quality and efficiency.
Higher Flexibility and Adaptability
Laser cutting is a very flexible and adaptable cutting method. It can cut almost all materials, cut parts of various shapes and sizes, and is suitable for many different applications.
Higher Environmental Friendliness and Safety
Laser cutting is a very environmentally friendly and safe cutting method. It does not produce waste gas, wastewater, or waste residue, and does not generate noise or radiation. This makes it a very popular cutting method.
Conclusion
When choosing a steel cutting method, multiple factors need to be considered, including material type, thickness, cutting precision requirements, cost, and production efficiency. Each cutting method has its advantages and disadvantages, and the choice should be made based on the specific situation.
If high cutting precision and smooth cuts are required, laser cutting or plasma cutting are better choices, but at a higher cost. If thicker materials need to be cut, plasma cutting or flame cutting can be considered, but the cut quality is lower and secondary processing may be required. If cutting precision is not a high priority, mechanical cutting can be chosen as it is lower in cost, but the cut quality will also be poor.
Considering all these factors, you can choose the steel cutting method that best suits your needs based on the specific situation.